IOT
DIGITAL TWIN
Operational efficiency of assets with Digital Twin
Integrating IoT technologies to build Digital Twins and drive operational efficiency
Digital Twin is a virtual replica of a product, service or process that simulates the behaviour of its physical counterpart, allowing it to be monitored, simulating its behaviour based on the past and predicting its behaviour in the future, automating the response actions to abnormal situations, also managing to maximise its efficiency.
neuroons takes the Digital Twin Instance and Aggregate approach: statistical modelling based on historical observations of a system.
To build a Digital Twin you need more than an IoT Platform to capture and store data. We can help you to implement the best information model to represent your assets and ease the making of optimization and predictive models. And as visuals matters we have broad experience building interactive visual representations that give near real time evolution of all dimensions, from unique device to aggregated views of your assets.
From connected devices to intelligent assets
With a secure virtual representation of all your connected physical assets, you are ready to improve your processes or even transform your entire business model.
Nowadays, the state-of-the-art of IoT means we have field devices or gateways which improved storage and computing capabilities, and this opens the door to shifting part of the processes to the end where the data is generated.
Digital Twin Competitive Advantages
01
Remote evaluation of performance in real-time operation.
02
Improve asset management, boost the efficiency of complex systems, and ensure product reliability and safety.
03
Predictive maintenance to anticipate actions and avoid downtime.
04
Simulation of scenarios by experimenting with boundary conditions to extract operating recommendations.
Industry Uses Cases
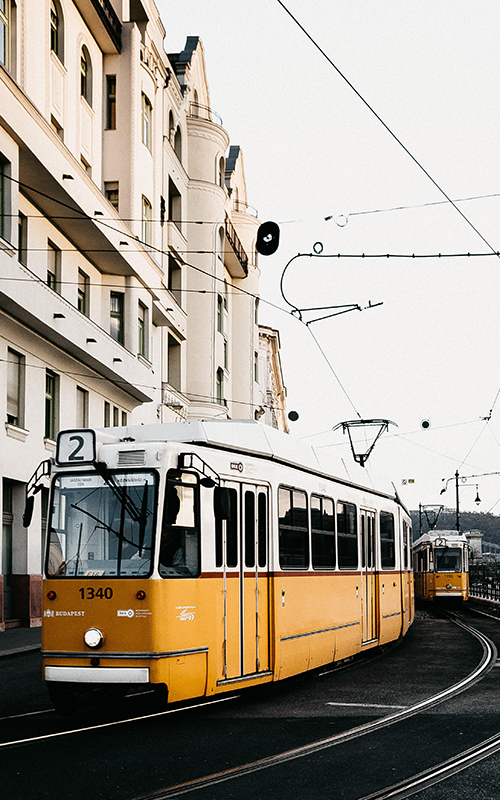
Smart Mobility
Smart Railway – Operational efficiency of rail transport fleets
A Digital Twin aggregates make real-time operation of vehicle fleets easier and provide data-driven mechanisms for their maintenance.
A Digital Twin allows advanced Smart Mobility solutions to be built based on ticketing, occupancy information and environmental information (weather, social events, seasonality, etc.), we can predict demand very precisely at any given time to adapt the necessary capacity.
The telemetry generated by each vehicle allows us to monitor it in real time and gather historical data with sufficient depth to use predictive techniques on its behaviour, and build models to optimise operation and maintenance.
Models can be trained to predict the deterioration of critical parts (those subject to friction and wear), monitoring their degradation (through vibrations and temperatures, for example) to anticipate, based on telemetry data, the planning of all the resources involved in their replacement (workshop, mechanics, machinery, etc.) with sufficient time in advance.
Smart Utilities
Wind turbine monitoring
Wind turbines serve as a source of continuous information on operational data (power generated, percentage of capacity covered, current operating status, ice on blades, etc.).
A Digital Twin for wind farms will allow real-time monitoring of the status of all assets and remote operation from a single operation centre. Based on operational information and external data sources (weather and forecast), machine learning techniques allow modelling behaviour and predicting energy generation in the short term.
Emission forecasting
The data analytics approach in the context of Digital Twin Instance allows the construction of predictive models of pollutant emissions in industrial equipment.
The use of Artificial Intelligence techniques to build the estimators represents a significant cost saving compared to the cost of equipping all the equipment with the sensor measurement load.
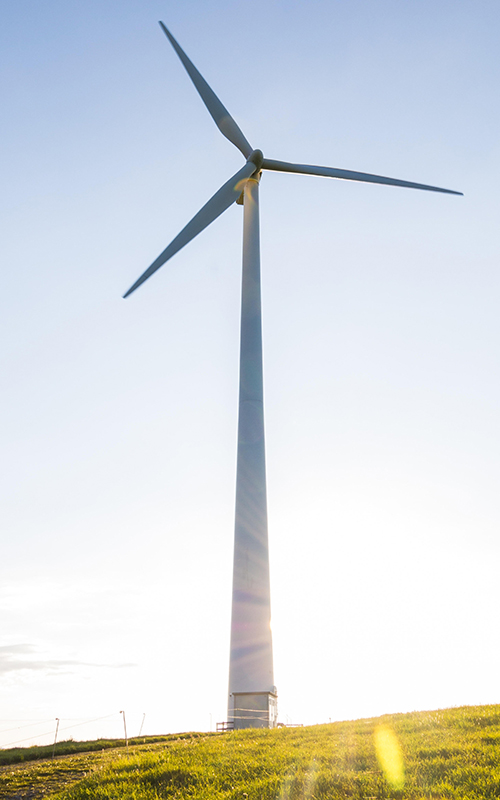
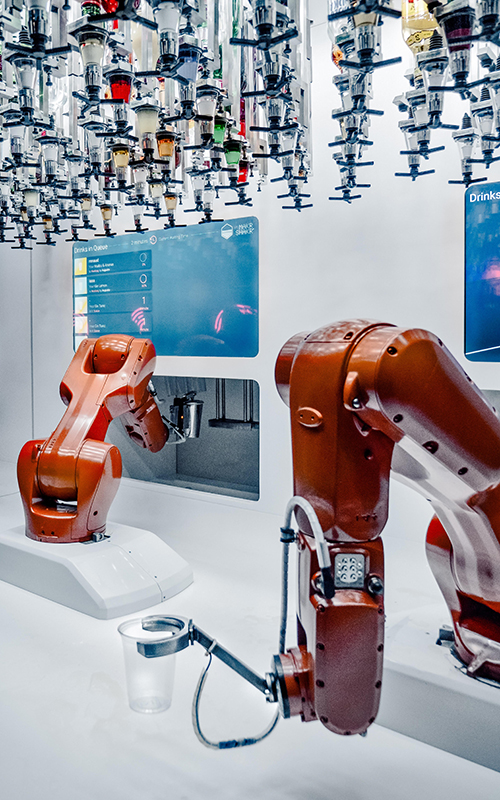
Industry 4.0
Quality on the production line
A Digital Twin, which is updated in real time with real data from machines and processes, makes it possible to study the impact of the variation of different parameters and conditions for the whole system.
By incorporating images of the process, live analysis of the quality of the manufactured elements (thermographic images of welds and hot forming) can be carried out. The analysis of the post operational data allows the diagnosis of the impact of the applied configurations on the resulting quality.
Energy efficiency
Monitoring the energy control system allows the detection of faulty operating states that often decrease the efficiency of the entire system.
New prognostics approaches for energy systems using AI-based techniques allow significant reductions compared to conventional control systems.